INNOVATION
Designing for the future
Using recycled shower water to flush toilets is one significant step towards “future-proofing” new homes says Geranium Corporation housing division president Boaz Feiner.
Every time you flush the toilet, it’s like 6 to 10 cups of drinking water are being flushed down the drain,” he points out. “Fresh drink-ing water is precious and it’s time to think about our relationship with this scarce re-source. A household system that re-uses and recycles greywater makes a lot of sense.”
As part of Geranium’s commitment to innovation, 18 homes at its Copperstone community in Ballantrae, in the town of Whitchurch-Stouffville, north of Toronto, will be built to accommodate a greywater recycling system. This uses daily shower and bath water to flush toilets. The system could result in a savings of 30 per cent in household water consumption — or hundreds of dollars a year, depending on the number of residents.
“That’s very substantial,” notes Feiner.
“Technology is changing so quickly,” he con-tinues, “and we want to be a leader in our business, rather than playing catch-up.”
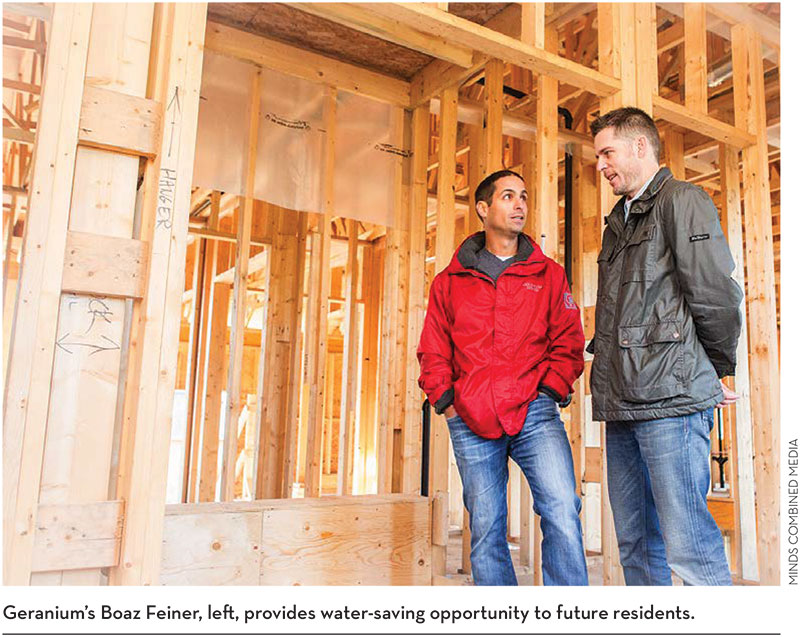
“Future-proofing” homes with state-of-the-art technologies, like smart wiring, solar-panel rough-ins and high-performance insu-lation will make homes energy-efficient and better prepared to meet the future demands of its homeowners.
Geranium is poised to be a leader in the greywater recycling field, the first Ontario residential builder to introduce such a sys-tem at a large-scale development.
While greywater systems are becoming common in commercial development, in the residential market they’ve mostly been found in high-end custom-built “green homes.” A system for use in the wider residential market is currently under devel-opment by Greyter Water Systems Inc., a Mississauga-based company that sells industrial-grade greywater recycling sys-tems for commercial use around the world, including Canada and the U.S. Among Greyter’s current project partners are the U.S. Army, Canada’s Department of Na-tional Defence and the Ontario Ministry of Education.
Geranium’s Copperstone development — which qualifies as an Energy Star for New Homes neighbourhood — will be a pilot project for Greyter’s residential greywater recycling system.
The first step will be the installation of plumbing in the homes at Copperstone to accommodate the system. The main shower and bath drains will be connected, so the greywater — defined as wastewater from washbasins, showers and baths — will run down to the system’s holding tank. From this tank, supply lines will connect to the toilets, providing recycled greywater to be used for flushing. All the required plumbing will be in place
COPPERSTONE
This cul-de-sac community of 18 manor homes — located in Ballantrae, in the town of Whitchurch-Stouffville, about 60 km north of Toronto — is Geranium’s newest Energy Star for New Homes neighbourhood. Each lot is approximately half an acre. Bungalows range in size from 2,990 to 3,732 sq. ft., and two-storey homes from 3,164 to 5,058 square feet. Prices start from $1.1 million. These homes are close to schools, golf courses and equestrian centres.
Drop by the presentation centre at Forest Trail Estates (on the west side of Hwy. 48, south of Aurora Rd.). For more information and hours of operation, phone 905-642-1900 or visit geraniumhomes.com.
whenever Greyter’s sytem is approved for production, likely within a year or so, according to John Bell, the company’s vice-president of business development.
“The prototype is built and in my home and working beautifully,” Bell reports. A greywater recycling system can save the av-erage household a considerable amount on their water bill, Bell notes. “If you’re a family of four to six, you can save — based on today’s 6-litre toilets — 60,000 to 90,000 litres of wa-ter a year.”
That’s almost $250 to $300 a year, he says. “And the cost of water is expected to go up every year,” he adds, “so there’s a significant savings opportunity here.”
The way Feiner sees it, the inclusion of the plumbing for a future greywater recycling system at Copperstone underscores the obvious advantage of buying a brand-new home.
“We feel it is our responsibility to take the first step to saving water on behalf of the future Copperstone homeowners. And we’ll encour-age them to take the next by having a complet-ed system installed,” says Feiner.
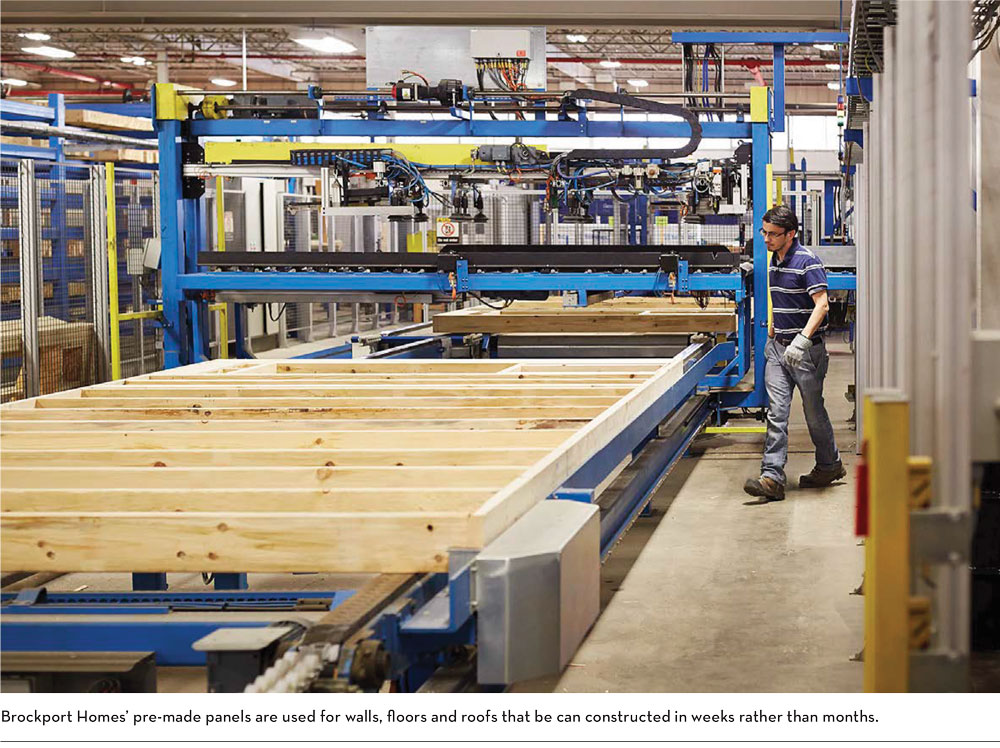
Precision panelling
Winter is fast approaching, and Louie Morizio, vice president of con-struction at Geranium Homes, is pleased that Uptownes in Stouffville is his next project. That’s because Uptownes, the latest phase of The Neighbourhoods of Car-dinal Point Geranium’s master-planned ra-vine community, can be built quickly using factory-made panels.
Each block of townhomes in the Uptownes enclave community will be constructed with panels manufactured in a controlled environ-ment. These components, which are designed to accommodate the homes’ plumbing, ventilation and electrical systems, will be delivered to the site and lifted into place with a boom truck, with assistance from a small crew. This will comprise the complete shell of a home in a fraction of the time it would
take to build a conventional stick-frame structure.
“With our winters, taking the weather fac-tor out of the equation means we can be more accurate with our timeframe,” says Morizio. “Now, instead of it taking two months to put up a block of townhomes, we can do it in ap-proximately two weeks.”
New way of building
Using pre-made manufactured panels is an-other example of how Geranium is embracing innovation to solidify its position as a leader in the home-building industry in the GTA.
“This is the way of the future,” says Morizio. He’s referring to wall, floor and roof panels as representing the next stage in home-construction evolution, from man-made on-site to prefabricated. It’s a shift that began with trussed roofs, expanded into engineered floor-joist systems and is now cul-minating in factory-made floor and wall panels. “You
can’t bury your head in the sand,” he says. “Change is coming, whether you like it or not, and you either embrace it or you fall behind.”
The first block of Uptownes townhomes at Cardinal Point will be constructed entirely with panels, including the walls, floors and roof. The computer-controlled system used to fabricate panels improves efficiency and minimizes errors in the construction process.
“We’re bringing the level of precision you would expect from the automotive or elec-tronics industry into the world of home-building,” notes Richard Wilson, president of Brockport Home Systems.
His Etobicoke-based construction com-pany is one of the manufacturers in current discussions with Geranium to build panels for Uptownes. “Houses that use our panels have better fit and finish,” says Wilson.
“Materials like ceramic tile, cabinetry and trim work will
UPTOWNES
This enclave of 134 homes will be built in phases. Home purchasers can choose between the Chicago Series of back-to-back townhomes and The Gooderham Series of stacked units. Unit sizes range from 1,401 to 1,639 sq. ft. The large rooftop terraces range in size from 279 to 380 sq. ft.
Drop by the sales centre on Millard St. (east of Hwy. 48 and north of Stouffville Rd). For more information and hours of operation, phone 905-640-9999 or visit geraniumhomes.com.
be straighter and more square.”
Manufactured panels also don’t generate much waste. “We reclaim and recapture all the waste at the factory,” Wilson explains.
From the method used to install pre-made panels, which results in minimal waste on the construction site itself to reduced fossil-fuel consumption in transporting labour and materials, Wilson says that there are many efficiencies and benefits to the builder, the end-owner and the environment.
Panel systems typically require more up-front investment than conventional construction; however, these costs are offset by downstream benefits, according to Wilson.
“The improvement you get in efficiency, speed, accuracy and precision — all that goes together to more than outweigh any extra hard dollar costs.”
Besides, Wilson adds, as the use of panels becomes more commonplace, their cost will approach that of conventional construction.
Geranium will pay careful attention to how the use of manufactured panels pan out at Uptownes.
The company is planning to use a similar system at its master-planned resort devel-opment, Friday Harbour, on Lake Simcoe in Innisfil, an area, Morizio points, out that’s known for its winter weather.
“Whichever company we choose to part-ner with at Uptownes, their knowledge and experience will be invaluable to us.
“I forsee this building project going smoothly and look forward to using panels wherever possible in future communities,” Morizio says.
“It makes sense for us and for the home-owners who will benefit from our ability to have increased accuracy in our construction timelines and even fewer after-sales-service items.”